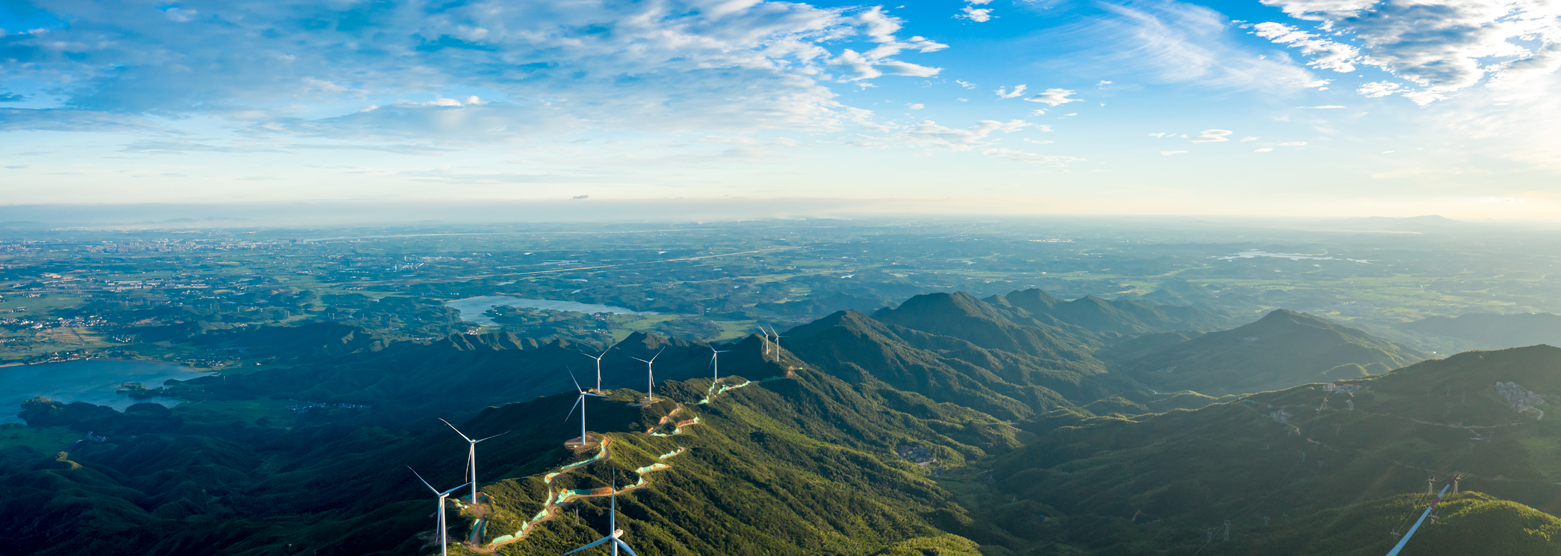
When it comes to growth, we believe in the
POWER OF ONE
While the rest of the world seems intent on growth through mergers, Covington Aircraft Engines remains true to the power of one: You. We are one family. Servicing engines from one manufacturer. With one guiding commitment. And by providing uncompromising service with core values first established by the Abbott family, we’ve built Covington Aircraft Engines over the last 50 years, one customer – and one engine – at a time.
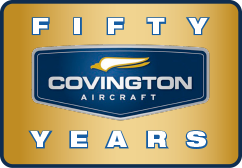
We’re honored to be celebrating our 50th Anniversary. It’s a longevity that would not be possible without you, our customers, and the trust you place in us each day. We deeply appreciate your patronage, your friendship, and your confidence in the work we do. It is a privilege to serve, and to do so without compromising our faith, nor our belief in our fellow man. Thank you again from all of us. And here’s to the next 50 years.
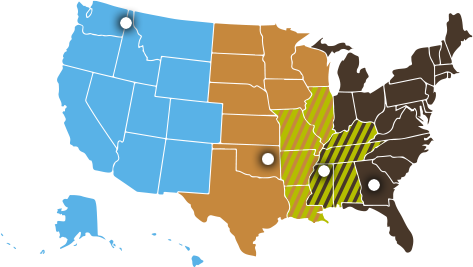
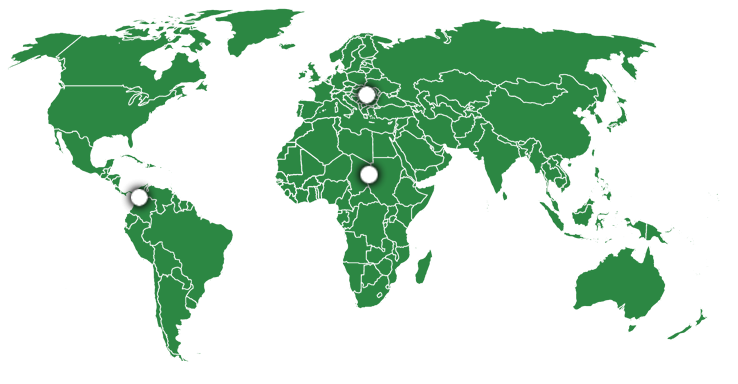
Find your sales representative
What sets Covington apart is the one-on-one relationships we build with our customers. We’re a family-owned company and we sincerely think of our customers as extended family members. And that’s not just talk. You can feel the Covington difference for yourself by reaching out to a sales representative. You’ll find out what we mean when we say we’re an engine facility – and a group of real people – like none other.
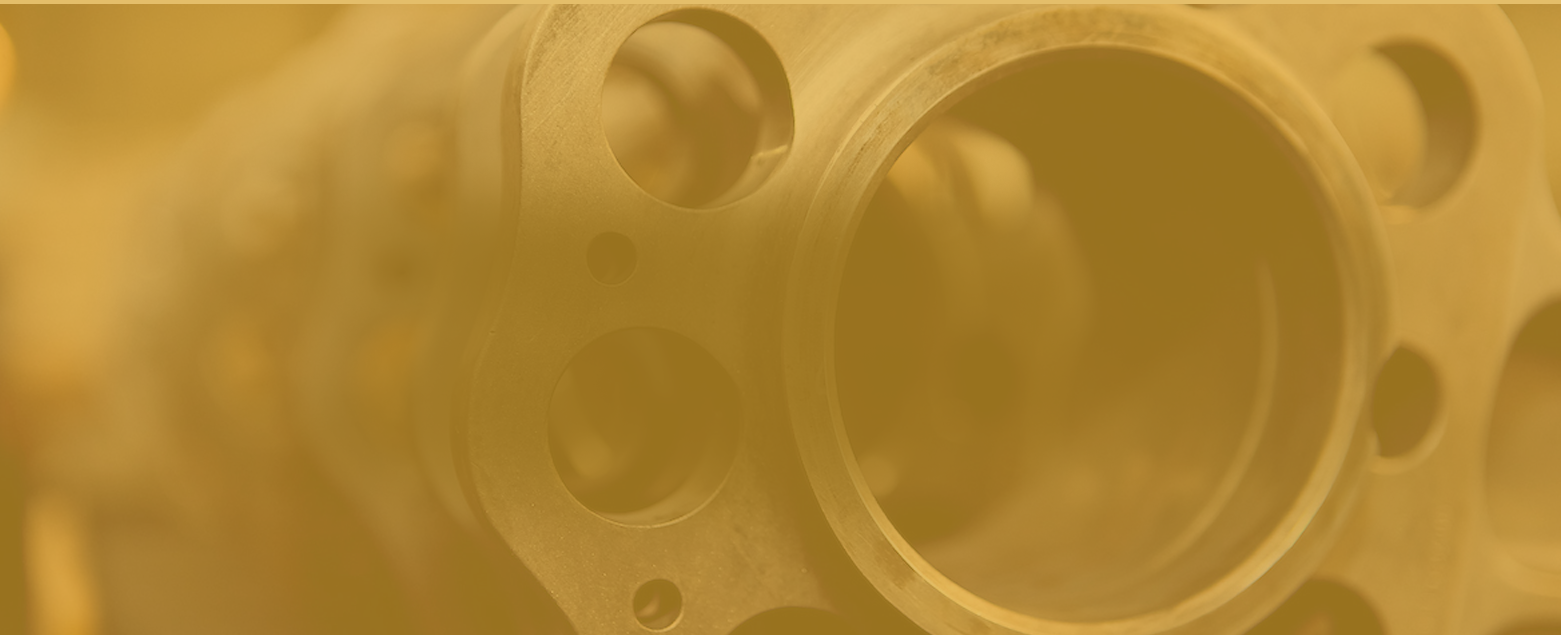
A message from our family to yours
The Abbott family’s story is one of the American Dream, sacrifice for country and our fellow man, and ethically focused decisions built around four key principles: Integrity, Dependability, Affordability, and Quality. As a result, Covington is a company grounded in old-fashioned family values which we strive to apply every day. It enables us to provide engine services with a level of personal trust and compassion you simply won’t find anywhere else. Come see us whenever your travels bring you our way. Or give a call and let us tell you more. Either way, it will always be our privilege to serve, and to have you become a part of our company’s family.
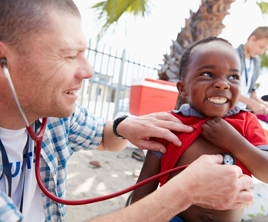
We support mission work
After becoming one of Covington’s first employees back in 1972, Paul Abbott went on to purchase the company with his wife Betty a few years later. Prior to that, Paul and Betty were missionaries, and they continued that calling without pause as owners of Covington Aircraft Engines. Today, led by Paul and Betty’s son, Aaron, our company continues to support missions around the world both personally and financially. A percentage of our profits go to support missionaries and their work each year, and mission aircraft are always serviced at a discount.
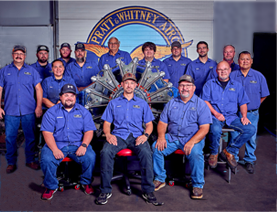
Engine repair from a family company
Covington Aircraft Engines specializes in Pratt & Whitney PT6A turbine and R-985 and R-1340 radial engines, with a full suite of supporting services and inventory. Today, we’re celebrating our 50th year in business, and have grown each year to become a world leader – and the only U.S.-owned Designated Overhaul Facility.

Sign up to receive the latest
Covington news
As Pratt & Whitney engine experts, we stay on top of what’s going on with engine trends, developments that are coming down the pike, and other news and tips that are directly helpful to you and your flight department. We’d love to share this intel to you
– all you need to do is sign up!

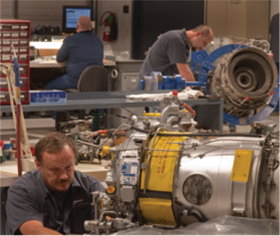
Expert field service delivered worldwide 24/7
Turbine or Radial, when your aircraft goes AOG, we go to you. 24 hours a day, worldwide. Our AOG Mobile Repair Team stands ready to get your aircraft back to flight readiness as quickly as possible. If your aircraft is AOG, call 918-756-7862.
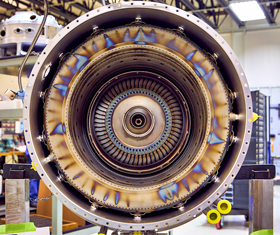
Find your Service Center
Whether it be parts support, technical advice, or full-on maintenance work – a spirit of service permeates every action we take at Covington. Our home base in Okmulgee, Oklahoma is ready to serve you. Or, should you need service in the field, our AOG Service Teams are on call 24-hours a day to come to your location. And regardless of being at our facilities, or in the field, we are standing-by to serve you. And to do so better than anyone else in the industry.
Okmulgee, Oklahoma: (918) 756-7862